Cargo lift factories are specialized facilities focused on the production and assembly of cargo lifts—essential equipment for efficiently moving heavy and bulky goods in various settings. These factories play a crucial role in industries such as logistics, manufacturing, retail, and more. This article explores the operations, technologies, and considerations involved in cargo lift factories Cargo Lift factory
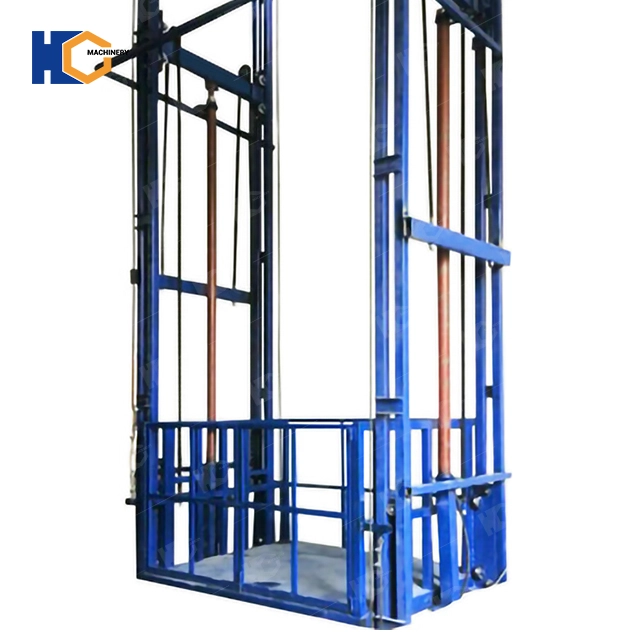
Key Functions of Cargo Lift Factories
- Design and Development:
- Custom Solutions: Factories collaborate with clients to design cargo lifts that meet specific requirements, including load capacities, dimensions, and features tailored to different applications.
- Prototyping: Engineers create prototypes to test design concepts, ensuring they meet performance and safety standards before proceeding with full-scale production.
- Manufacturing Process:
- Material Selection: Factories select high-quality materials like steel, aluminum, and stainless steel for their durability and suitability for heavy-duty applications.
- Fabrication: Components are fabricated using advanced machinery. This involves cutting, welding, and assembling parts such as lift shafts, platforms, and support structures.
- Assembly: Assembled components are integrated into a complete cargo lift system, ensuring all parts fit together seamlessly and function correctly.
- Testing and Quality Control:
- Performance Testing: Cargo lifts are subjected to rigorous performance tests to verify their ability to handle the specified loads and operate efficiently under various conditions.
- Safety Inspections: Comprehensive safety inspections ensure that the lifts comply with industry standards and safety regulations.
- Quality Assurance: Continuous quality control measures are implemented to maintain high manufacturing standards and address any potential issues.
- Installation and Support:
- Site Preparation: Factories often assist with site preparation, including structural modifications and electrical work required for the lift installation.
- Installation: Experienced technicians handle the installation process, ensuring proper setup and integration with existing systems.
- Maintenance: Many factories offer maintenance services, including regular inspections, repairs, and upgrades to ensure the lift’s long-term performance and reliability.
Technologies in Cargo Lift Factories
- Manufacturing Equipment:
- CNC Machines: Computer Numerical Control (CNC) machines are used for precise cutting and fabrication of lift components.
- Robotic Systems: Robots assist in accurate welding and assembly tasks, ensuring consistency and precision.
- Design and Simulation Software:
- CAD Systems: Computer-Aided Design (CAD) software is utilized to create detailed designs and simulations of cargo lifts.
- Simulation Tools: Advanced simulation tools test and optimize designs before they are physically produced, ensuring they meet performance requirements.
- Control and Safety Systems:
- Automation: Modern cargo lifts incorporate automated control systems for efficient and smooth operation.
- Sensors and Monitoring: Integrated sensors and monitoring systems provide real-time data on lift performance, ensuring safe and reliable operation.
Considerations for Cargo Lift Factories
- Regulatory Compliance:
- Safety Standards: Factories must adhere to safety regulations and standards set by organizations such as ANSI (American National Standards Institute) and CEN (European Committee for Standardization).
- Certifications: Obtaining necessary certifications ensures that cargo lifts meet industry standards and regulatory requirements.
- Customization Capabilities:
- Adaptability: Factories should be capable of accommodating custom designs and modifications to meet specific client needs.
- Flexibility: The ability to adjust manufacturing processes to produce various types of cargo lifts is crucial for addressing diverse requirements.
- Sustainability:
- Environmental Impact: Factories should implement sustainable practices and use eco-friendly materials to minimize their environmental impact.
- Energy Efficiency: Incorporating energy-efficient technologies and processes can reduce the carbon footprint of manufacturing operations.
- Customer Support:
- After-Sales Service: Providing robust after-sales support, including maintenance and repair services, is essential for ensuring customer satisfaction and equipment longevity.
- Training: Offering training on the operation and maintenance of cargo lifts enhances usability and extends the equipment’s lifespan.
Leading Cargo Lift Manufacturers
- Otis Elevator Company: Known for its high-quality cargo lifts and innovative solutions, Otis provides customizable options to meet various needs.
- Thyssenkrupp: Offers a range of cargo lifts with advanced technology and flexible design options.
- KONE: Specializes in modern cargo lifts with a focus on efficiency, design flexibility, and technological integration.
- Schindler Group: Provides reliable cargo lifts with a strong emphasis on quality control, safety, and comprehensive customer support.
Conclusion
Cargo lift factories are integral to the manufacturing and supply of cargo lifts, combining advanced technology, engineering expertise, and rigorous quality control to deliver effective solutions for heavy goods transport. By focusing on design, manufacturing, and support, these factories ensure that cargo lifts meet high standards of performance and safety. Understanding the operations and considerations involved in cargo lift factories helps businesses make informed decisions and choose the right solutions for their specific needs Cargo Lift factory